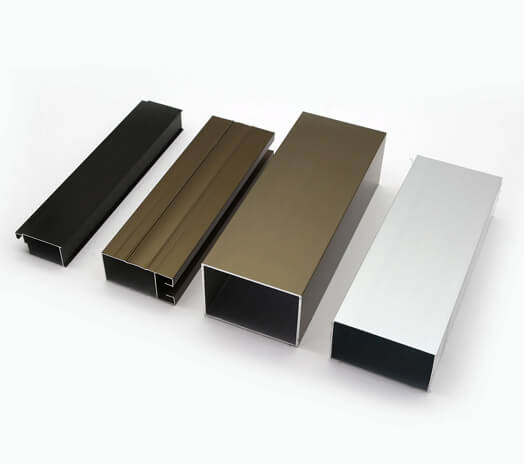
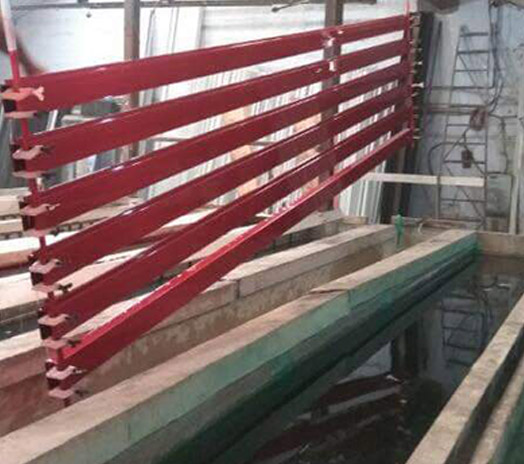
What is Anodizing?
Anodizing is the successful development and control of a natural oxidation process that occurs when aluminium is exposed to the atmosphere.
Electricity and chemicals are used jointly to recreate this natural process, producing a hard, transparent surface layer that is integral with the base aluminium. This layer increases resistance to corrosion, as the process of anodizing stops the natural oxidation in the aluminium. It can vary in thickness (10 - 25 μm), providing different levels of protection from the atmosphere, with different requirements based on its surroundings.
Why Anodize?
Aluminium is anodized for corrosion resistance, abrasion resistance, and insulation from electricity, adhesion, or aesthetic enhancement.
This gives the aluminium the following characteristics:
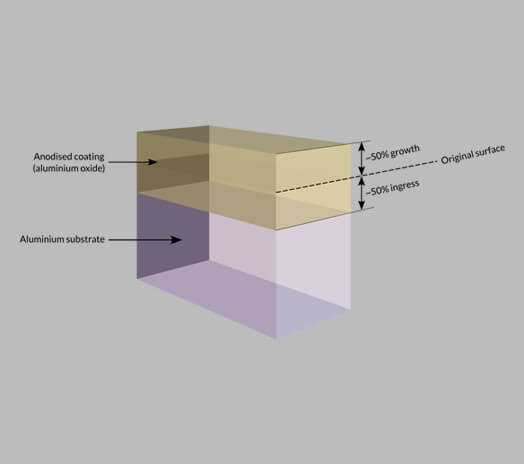
The Anodizing Process
Batch (or piece), sheet, and coil anodizing all consist of three processing stages:
Pre-treatment
The aluminium surface is first cleaned then chemically treated. Etching results in a matte appearance. Various degrees of etching can be specified (i.e. light, medium, heavy), producing in a slightly different visual end result.
Anodizing
Once the surface is prepared, the anodic film is built. Electrical current is passed through an electrolyte bath in which the aluminium has been immersed. The anodic film is built from the aluminium itself, not applied and is hard and porous. The coating thickness is tightly controlled, with 10, 15, 20 and 25 microns (μm) available as options based on the end use product. The thicker the anodic film, the more protection to the base aluminium is offered, with certain uses carrying a minimum requirement (i.e. anything nears the coast should be 25μm). We also offers a warranty grade 25μm service to ensure peace of mind for the end user.
Colour (optional) & Post Treatment
The porous anodic film can be coloured in this stage. Organic dyes can be used to fill pores with colour, or metal salts can be electrochemically deposited at the base of the pores to create a broad spectrum of colours. Many of the colours are fade-resistant. Sealing the anodic film normally consists of a hot water bath that basically swells the pores shut.
Pranav Anodize Samples
Standard Colors ( Note - Actual anodize colors may vary from on-screen and printer representations. )